Карбон: мебель и предметы обихода из углеродного волокна | Admagazine
Материал, символизирующий торжество передовых технологий, на самом деле придуман давно – еще в 1880 году Томас Эдисон предлагал делать из углеродного волокна нити накаливания для своих ламп. Однако в отличие от лампочек эта новация ждала своего часа больше века.
Углепластик, композитный материал из переплетенных нитей углеродного волокна, скрепленных с помощью эпоксидных смол.
LEGION-MEDIA; АРХИВЫ ПРЕСС-СЛУЖБЗато теперь углеродное волокно (или попросту карбон, от английского carbon fiber) встречает нас повсюду: его используют в космической индустрии и самолетостроении, делают из него кузовные детали автомобилей и протезы – пара карбоновых ног принесла бегуну-инвалиду Оскару Писториусу шесть золотых медалей на Паралимпийских играх. Примеры применения углеродного волокна в дизайне пока штучные, но яркие.
Электровелосипед с рамой и рулем из углепластика LEAOS 2.0 Carbon City Design E-Bike, LEAOS.
Чаще всего карбон встречается в виде углепластика, композитного материала с эффектом 3D. Именно это свойство привлекло часовую марку IWC. “Благодаря углеволокну корпус часов отличается сложной трехмерной геометрией”, – говорит креативный директор компании Кристиан Кнооп, отвечавший за разработку коллекции Ingenieur Automatic Carbon Performance.
Часы Ingenieur Automatic Carbon Performance с корпусом и безелем из углепластика, IWC.
LEGION-MEDIA; АРХИВЫ ПРЕСС-СЛУЖБК тому же в часовом деле традиционно ценится не только конечный результат, но и трудоемкость самого производственного процесса. Карбон в этом смысле – идеальный выбор: корпус часов состоит из 45 деталей от 0,1 до 0,3 мм толщиной, вручную уложенных в форму для прессования. Сотрудникам IWC даже пришлось изобрести новый способ обработки карбоновой ткани.
Диван ONYX из углеродного волкна и вулканического камня, разработанный в рамках экспериментального проекта Peugeot Design Lab.
Голландский дизайнер Марсель Вандерс, который начал делать карбоновую мебель одним из первых, тоже ссылается на тягу к экспериментам: “Мне нравится придумывать новое применение для хорошо известных материалов”. Дизайнер ценит углеводородное волокно за сочетание прочности и легкости – придуманный им в 2004 году Carbon Chair весит всего 3,7 кг. “Материала требуется меньше, отходов тоже получается меньше, а служит такая вещь дольше”, – говорит Вандерс.
Стул Carbon Chair, дизайн Бертьяна Пота и Марселя Вандерса для Moooi.
LEGION-MEDIA; АРХИВЫ ПРЕСС-СЛУЖБСейчас, по словам дизайнера, у него в работе целый гарнитур карбоновой мебели. “Это материал, который почти не подвержен влиянию времени, он и через сто лет будет выглядеть так же, как сегодня, – рассказывает он. – А мне хочется делать вещи, которые вызывают у людей душевную привязанность и желание никогда с ними не расставаться”.
Чехол для костюма из углепластика — один из четырех предметов багажа, разработанных Louis Vuitton для автомобилей BMW i8.
Топор Core Axe с топорищем из углепластика и лезвиями из высокоуглеродистой стали по дизайну Каспера Гамильтона для Zai.
LEGION-MEDIA; АРХИВЫ ПРЕСС-СЛУЖБТекст: Анастасия Ромашкевич
Фото: LEGION-MEDIA; АРХИВЫ ПРЕСС-СЛУЖБ
Что такое карбон и его модульность?
«
Три крупнейших японских завода, производящие карбон: Toray, Mitsubishi и Toho
«
В настоящее время у производителей всех известных марок спиннингов обязательно присутствуют модельные ряды из карбона (углепластика, графита). Бланки спиннинговых удилищ производятся из особой ткани, которая состоит из нескольких слоев тончайших углеродных нитей, плотно сплетенных со связующим композитным материалом, и расположенных под специальными углами по отношению друг к другу. Эта ткань получается высокопрочной и жесткой, но в то же время очень легкой. Само волокно бывает нескольких видов, и важную роль играет связующий композитный материал.

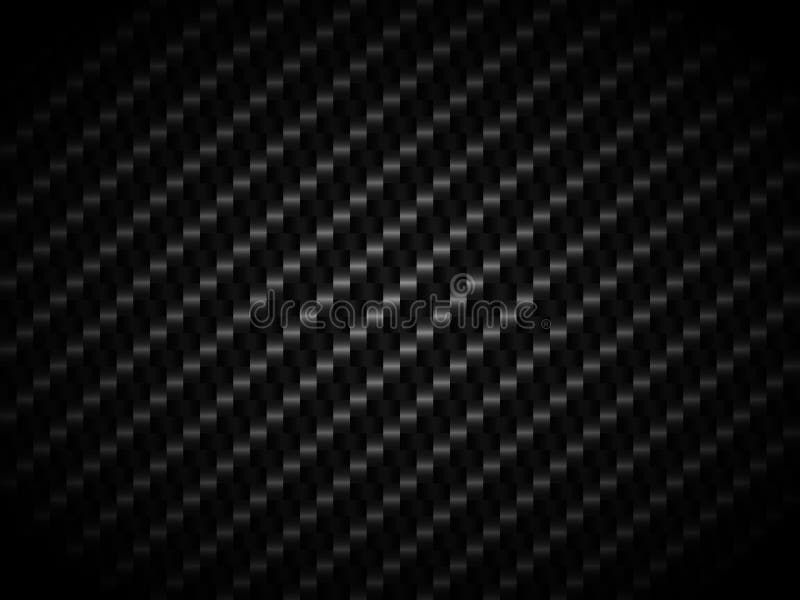
В заключение хочется добавить, что не стоит выбирать спиннинг только исходя из марки или модульности карбона, необходимо смотреть на строй, тест, ручку и насколько вам удобно будет ловить данным орудием.
Карбон — уникальный материал для тюнинга
Возможно, кто-то из читателей слышит о слове карбон впервые, некоторые же вовсе наделяют это понятие не относящимся к нему значением. Пришло время раскрыть все карты и познакомиться с этим материалом для тюнинга.
Происхождение карбона
Эта вариация композитного материала складывается из тончайших углеродных нитей, сплетенных вместе подобно элементам стержня в грифельном карандаше. За сцепления компонентов материала отвечают эпоксидные смолы. Ломаются подобные нитевидные образования легко, но порвать их практически невозможно. Из них плетут полотно елочкой или рогожей, выбирая тот рисунок, который более актуален для ткани. Максимальная прочность достигается за счет накладывания одного слоя полотна на другой. Причем направление плетения в слоях чередуется. Крепятся ткани друг к другу посредством эпоксидной смолы.
Спойлеры, выполненные из карбона
Рассмотрим плюсы использования:
- прочность, сравнимая с металлом и превосходящая стекловолокно;
- малый вес материала (карбон на 2/5 уступает в весе стали и на 1/5 — алюминию).
Отсюда ясно почему кокпиты болидов Формулы 1 изготавливаются из этого композитного материала.
Попробуем рассмотреть минусы карбона:
- высокая ценовая категория, превосходящая затраты на производство деталей из стекловолокна;
- материал боится локальных ударов и может со временем превратить капот автомобиля в решето при попадании камней;
- подвержен выцветанию на солнце;
- невозможность частичного ремонта, деталь из карбона необходимо заменять целиком.
Как и остальные материалы для тюнинга карбон требует основательного ухода. Однако его производительность и потенциал до сих пор применяются с привилегией в автоспорте. Это пока единственный материал, который выдает реальные показатели прочности при максимально возможной легкости деталей.
Статьи — Краткое описание композитных материалов.
STEEL fiber (Металлик)
Материал нового поколения для производства композитных конструкций. Отличается оригинальным дизайном. По своим свойствам близок материал не много уступает карбону.
СТЕКЛОВОЛОКНО
Этот материал уже давно применяется при строительстве лодок, катеров, яхт и много другого. Стеклоткани (стеклорогожа) используются для придания жесткости и объема готовому изделию. Стеклоткань/стекловолокно это на самом деле стекло, вытянутое в очень тонкие волосообразные волокна. Отдельные волокна соединяются в нити и, затем, из нитей плетётся ткань. Является композитным материалом. Для изготовления весел и лодок мы используем стекловолокно класса Е (E-glass).
КАРБОН
Карбон — композитный материал, относится к классу углепластиков. Основу углетканей составляют тонкие нити углерода. Сломать нить просто, но порвать очень нелегко. Углепластиковые детали легче и прочнее стеклопластиковых. В производстве весел и лодок карбон позволяет добиться максимум прочности и жесткости при минимальном весе. Стоит сказать и о недостатках, а они, к сожалению, есть. Карбон имеет очень маленькое относительное удлинение, т. е. не растягивается.
АРАМИД или КЕВЛАР
Марка KEVLAR принадлежит известной американской корпорации DuPont. Этот материал был изобретен в 1965 г. учеными компании Стефанией Кволек и Гербертом Блэйдсом. Kевлар/арамид представляет собой паpааpамидовое (paraaramid) синтетическое волокно. Эти волокна состоят из длинных молекулярных цепей. Между собой цепи жестко сориентированы прочными внутренними связями, которые и определяют свойства кевлара/арамида. Kевлар/арамид – очень прочный материал, имеет высокую структурную твердость и как следствие малую степень растяжимости. К достоинствам кевларa/арамида можно отнести и следующее: низкая термическая усадка, высокое сопротивление на разрыв и порезы, небольшой вес.
КАРБОН-КЕВЛАР
Свойства карбона и кевлара/арамида давно пытаются объединить. В последнее время можно часто встретить гибриды карбон-арамид. Этот материал является промежуточным по своим характеристикам между карбоном и арамидом. Кроме того, чтобы полностью использовать все преимущества этих материалов, мы применяем вакуумные технологии, позволяющие снизить вес изделия на 30-40%, термообработку.
Все выше перечисленные композитные материалы нашли широкое применение при производстве кокпитов для болидов Формулы-1 и кабин самолетов, корпусов и мачт катеров и яхт, кузовных элементов, деталей внутренней отделки и даже рессор и карданов для автомобилей. По сравнению со стекловолокном это более дорогие материалы (в 4-5 раз).
Зачем нужен карбон?
Он на 75% легче железа и на 30% — алюминия, и при этом имеет прочность на разрыв в четыре раза выше, чем у лучших марок стали.
Сами по себе карбоновые нити довольно хрупкие, поэтому из них плетут гибкие и эластичные полотнища. При добавлении к ним связующих полимерных составов получают углепластики, которые совершили настоящий переворот в спорте, технике и многих других областях человеческой деятельности.
Карбон на дорогах, в небе и на море
Наиболее широко известная область применения карбона — это автомобилестроение. Вначале его выдающееся сочетание прочности и легкости заинтересовало конструкторов болидов Формулы-1, что позволило значительно снизить вес гоночных машин. Джон Бернард, инженер британского автомобильного производителя McLaren, впервые сделал элементы кузова из углеволокна в начале 1980-х гг. Это дало столь ощутимую прибавку в скорости, что сразу привело гоночную команду McLaren на призовые места.
Впрочем, право быть самым быстрым обходится весьма недешево из-за того, что все углепластиковые детали фактически изготавливаются вручную. Карбоновую ткань особого плетения выкладывают в литейные формы, затем соединяют полимерными составами. На заключительном этапе она подвергается обработке при высокой температуре и давлении. Поэтому долгое время карбоновые элементы кузова использовались только в суперкарах и моделях премиального класса. И лишь недавно анонсирован выпуск доступных широкой аудитории серийных моделей с углепластиковыми деталями. Так, в конструкции кузова нового BMW i3 будут широко представлены элементы из углеродного волокна. А в новой версии хэтчбека Volkswagen Golf GTI VII благодаря углепластиковым капоту и крыше удалось снизить вес машины сразу на 200 кг!
Еще более широкое применение материалы на основе карбона получили в авиастроении , где они начали теснить традиционные алюминий и титан. Первыми перспективы оценили авиаконструкторы, работающие в оборонной промышленности. Например, в новейших российских истребителях Су-47 и Т-50 используются углепластиковые компоненты крыла и фюзеляжа.
Все шире применяется карбон и в пассажирских самолетах, где он позволяет снизить расход топлива и повысить грузоподъемность. Так, в лайнере Boeing 787 Dreamliner не менее 50% элементов фюзеляжа изготовлены из композитных материалов на основе углерода, благодаря чему расход топлива снижен на 20%. С той же целью самый большой пассажирский авиалайнер Airbus А380 оснастили крыльями, которые на 40% состоят из углепластиков. А фюзеляж современного бизнес-джета Hawker 4000 почти целиком изготовлен из этого материала!
Не менее активно используется карбон и в кораблестроении. Причина популярности та же: уникальное соотношение прочности и веса, жизненно важное в суровых морских условиях. Кроме того, для корабелов ценны ударопрочность и коррозионная стойкость этого материала.
Как обычно, первыми начали применять углепластики в оборонной сфере. Из карбоновых композитов делают элементы корпусов подводных лодок, поскольку они серьезно снижают шум и обладают stealth-эффектом, делая судно «невидимым» для радаров противника. А в шведских корветах типа «Visbi» корпус и надстройки сделаны из карбоновых композитов по stealth-технологии. Используется многослойный материал с основой из ПВХ, которая покрыта тканью особого плетения из углеродных жгутов. Каждый такой жгут поглощает и рассеивает радиоволны от радаров, не давая обнаружить судно.
Для гражданских кораблей невидимость для радаров не нужна, а вот легкость, прочность и возможность изготавливать детали практически любой конфигурации оказались очень востребованными. Чаще всего карбон применяют при строительстве спортивных и прогулочных яхт, где важны скоростные характеристики.
Элементы будущего судна «лепятся» из углепластиковых холстов по компьютерной модели как из пластилина. Вначале делается полноразмерный макет палубы и корпуса из специального модельного пластика. Затем по этим лекалам вручную слоями выклеиваются полотнища карбоновой ткани, скрепляемой эпоксидными смолами. После просушки готовый корпус шлифуют, красят и покрывают лаком.
Впрочем, есть и более современные способы. Например, итальянская компания Lanulfi сумела почти полностью автоматизировать процесс.
Крупные конструктивные элементы судна с помощью 3D моделирования разбивают на более мелкие, но идеально совпадающие части. По компьютерной модели с помощью станка с программным управлением выполняются основы, которые и служат матрицами для выклеивания углепластиковых деталей. Такой подход позволяет добиться максимальной точности, что очень важно для ходовых качеств спортивных яхт.
Карбон для каждого
Карбон начинает все шире применяться и в строительстве. Добавление углеродных волокон в состав бетона делает его гораздо более устойчивым к внешним воздействиям. Фактически получается сверхпрочный монолит с очень плотной поверхностью. Такая технология применяется в строительстве небоскребов и плотин, а также при обустройстве туннелей.
Стоит упомянуть и материалы для усиления, ремонта и реставрации железобетонных поверхностей — специальные холсты и пластины из карбоновой ткани (например, Mapewrap или Carboplate). Они позволяют полностью восстановить конструкцию, не прибегая к дорогостоящей и не всегда возможной перезаливке.
Для крупных девелоперов и частных застройщиков особо интересна такая инновация, как применение карбона в штукатурной системе утепления фасадов.
«Добавление в армирующий состав мельчайших карбоновых волокон диаметром менее 15 микрон приводит к очень важному результату — многократному увеличению ударопрочности фасада, — говорит Роман Рязанцев, проект-менеджер компании CAPAROL, эксперта в области защиты и теплоизоляции фасадов зданий. — В частности, карбоновая добавка в штукатурную систему CAPATECT Carbon (Caparol) позволяет фасаду без вреда переносить удары с энергией до 60 Джоулей — это в десять раз больше, чем способны выдерживать обычные варианты штукатурных фасадов».

Если владелец коттеджа решит использовать такую систему для внешней отделки своего жилища, то он не только сократит затраты на отопление и обеспечит благоприятный микроклимат в помещениях, но и защитит стены от любых механических воздействий. Крупный град разбивает виниловый сайдинг и оставляет вмятины на обычной песчаной штукатурке. Шквалистый ветер, несущий с собой мусор и ветки деревьев, также может повредить фасад. Но на отделке с добавлением карбоновых волокон не останется ни следа. Тем более не страшны ей такие бытовые воздействия, как удары мячом или шайбой в детских играх.
«Обычно для защиты цокольной части фасада от случайных повреждений используют облицовку камнем, например, керамогранитом, — отмечает Даниил Мазуров руководитель отдела оптовых продаж московской строительно-торговой компании «ПКК Интерстройтехнологии».
— Но для отделки цокольной части жилого комплекса, который сейчас строится на юге Москвы, мы решили попробовать штукатурную систему с карбоном. В сравнительных испытаниях она показывала очень впечатляющие результаты».
Вадим Пащенко, руководитель направления WDVS Московского регионального отдела компании CAPAROL, называет еще одно ценное следствие применения в штукатурной системе армирующих компонентов с карбоновыми волокнами: фасад становится устойчив к температурным деформациям. Для архитекторов и владельцев частных домов это означает полную свободу в самовыражении — можно окрасить стены дома в любые самые тёмные и насыщенные цвета. С традиционной цементно-песчаной штукатуркой такие эксперименты могут закончиться печально. Темная поверхность стены слишком быстро нагревается под солнечными лучами, что приводит к образованию трещин на внешнем защитно-декоративном слое. Но для фасадной системы с карбоновыми волокнами подобной проблемы не существует.
Сейчас по всей Европе начинают появляться выделяющиеся на общем фоне частные коттеджи и коммерческие здания, школы и детские сады, которым карбон помог обрести выразительные и насыщенные цвета. По мере того как российские частные домовладельцы начинают экспериментировать с цветами фасадов, отходя от традиционных пастельных оттенков, эта инновационная технология становится востребована и в нашей стране.
Карбон для поколения Next
Без карбона ныне невозможно представить ни одну высокотехнологичную отрасль. Он становится все доступнее и для обычных людей.
Сейчас мы можем приобрести углепластиковые лыжи, сноуборды, горные ботинки, спиннинги и велосипеды, шлемы и прочую спортивную экипировку.
Но на смену ему уже идет новое поколение материалов — углеродные нанотрубки, которые в десятки раз прочнее стали и обладают массой других ценнейших свойств.
Так, канадский производитель одежды Garrison Bespoke разработал мужской костюм, который сделан из ткани на основе углеродных нанотрубок. Такая ткань останавливает пули до сорок пятого калибра и защищает от колющих ножевых ранений. Кроме того, она на 50% легче кевлара — синтетического материала, используемого для изготовления бронежилетов. Подобные костюмы наверняка войдут в моду среди бизнесменов и политиков.
К числу самых фантастических применений карбоновых нанотрубок относится космический лифт, который позволит доставлять на орбиту грузы без дорогих и опасных запусков ракет. Его основой должен стать сверхпрочный трос, протянутый от поверхности планеты к космической станции, находящейся на геостационарной орбите на высоте 35 тыс. км над Землей.
Эта идея была предложена еще великим русским ученым Константином Циолковским в 1895 году. Но до сих пор проект казался неосуществимым по техническим причинам, ведь не было известно материалов, из которых можно сделать настолько прочный трос. Однако открытие углеродных нанотрубок в начале 1990-х гг. заставило пересмотреть границы возможного. Сотканная из карбоновых нанотрубок нить миллиметровой толщины способна выдержать нагрузку примерно 30 тонн. А значит, дешевые и безопасные путешествия на орбиту в кабине космического лифта из фантастического сюжета превращаются в практическую задачу для инженеров.

Пресс-служба CAPAROL
Технологии
Инновационный материал в часовом искусстве: Карбон
В последнее время, в часовой индустрии наблюдается тенденция, следуя которой, бренды экспериментируют с материалами космической эпохи, которые выходят за рамки современного часового дела. От high-end композиций до кусков сапфира, сфабрикованных в корпус наручных часов. Эта практика, кажется, не собирается замедляться в ближайшее время. Одним из таких инновационных материалов является карбон (углеродное волокно), и сегодня мы глубже вникнем в новинки часов, не только корпус которых, но и составляющие, такие как механизм и архитектурные элементы, выполнены из этого материала.
На часовой выставке SIHH 2017 Roger Dubius представили новое дополнение к линейке Excalibur — Roger Dubuis Excalibur Spider Carbon. Используя карбон T700, Roger Dubius смогли уменьшить вес часов на 30%, что идеально для их 45 мм корпуса. В то время, как толстые карбоновые слои визуально привлекательны при наблюдении за конструкцией корпуса, Roger Dubius использовали концепцию и дальше. Мосты наручных часов, как и плато их механизма, а также верхняя клетка турбийона сделаны из карбона. В результате, часы выходят на новый уровень, речь идет уже не о каких-то трюках с целью победить в борьбе за рынок, а о чем-то большем, нежели мы ожидаем увидеть от углеродных материалов.
Другим карбоновым королем наручных часов является Panerai Luminor Carbotech 3 Days, также представленные на SIHH 2017. Помимо использования карбоновых нанотрубок. поглощающих свет для достижения глубокого черного контраста, мы можем обнаружить, что карбон играет гораздо большую роль в этих наручных часах от Panerai. Использование углеродной керамики и тантала практически устраняет необходимость в использовании традиционных смазочных материалов и драгоценных камней в механизме. Результат? Часы с механизмом, который не нужно обслуживать в течение 50-ти лет.
Не будем ходить вокруг да около — на SIHH 2017 следующие часы можно назвать Big Bad Boy. Имея вес всего 40 грамм (с ценой, близкой к $25,000 за грамм), сплит-секундный хронограф RM 50-03 McLaren F1 выносит карбон на какой-то экстремальный уровень. Наряду с использованием титана 5-го класса, Richard Mille решили использовать карбон TPT для мостов механизма и основного плато. В результате, это приводит к необычайно малой массе даже в совокупности с тканевым ремнем и корпусом, выполненным из графиносодержащей смолы, внедренной в слои углеродного волокна.
Поэтому, даже если карбон не является Вашим предпочтением, довольно очевидно, что нам придется чаще и чаще видеть на грядущих выставках часы, выполненные из этого инновационного материала. На самом деле, трудно жаловаться, да и не зачем. Такое исследование материалов является показателем того, что часовые бренды еще заинтересованы в освоении новых территорий, а не только специализируются на традиционных принципах часового искусства. Это то, что делает производство интересным и является отличным знаком того, что компании продолжают идти вперед и смотреть в будущее.
Серия Atlas Design, материал пластик, цвет механизмов Карбон
348983,a7587a37-a540-11e8-8121-000c29943515348985,b466f45b-a540-11e8-8121-000c29943515348988,d0ecdaf0-a540-11e8-8121-000c29943515348989,d8e5128e-a540-11e8-8121-000c29943515349219,545fee98-af69-11e8-8122-000c29943515351383,96f75835-2aad-11e9-812c-000c29943515348986,c32cc1a1-a540-11e8-8121-000c29943515348987,ca42fa55-a540-11e8-8121-000c29943515348990,e035bcf1-a540-11e8-8121-000c29943515349218,545fee96-af69-11e8-8122-000c29943515359533,4f90503a-0c2d-11ea-813f-000c29943515349000,1a4801d3-a541-11e8-8121-000c29943515349001,1a4801d5-a541-11e8-8121-000c29943515359523,80f2cfc4-0c2c-11ea-813f-000c29943515349717,98b55ce1-d2bb-11e8-8125-000c29943515348991,e035bcf3-a540-11e8-8121-000c29943515348992,eb26cd27-a540-11e8-8121-000c29943515349018,98cfffac-a541-11e8-8121-000c29943515359481,17762719-0c29-11ea-813f-000c29943515349216,545fee92-af69-11e8-8122-000c29943515359325,23c540b2-061f-11ea-813e-000c29943515348981,704a58f1-a540-11e8-8121-000c29943515359471,c33b7c79-0c28-11ea-813f-000c29943515348982,a7587a35-a540-11e8-8121-000c29943515348997,06ba3a36-a541-11e8-8121-000c29943515348998,0ebb245e-a541-11e8-8121-000c29943515348993,eb26cd29-a540-11e8-8121-000c29943515348994,f5c8d25f-a540-11e8-8121-000c29943515348995,f5c8d261-a540-11e8-8121-000c29943515348996,00960645-a541-11e8-8121-000c29943515348999,0ebb2460-a541-11e8-8121-000c29943515
углеродных материалов | Инженерные материалы для технологических нужд
«Область углеродных материалов огромна и часто трудна для понимания, но эта книга легко читается и методично охватывает предмет, включая представление свойств материалов и данных о характеристиках с четкими иллюстрациями и графиками. Ссылки включают соответствующие старые и современные — актуальные источники информации.Книга носит учебный характер и является отличным ресурсом для студентов старших курсов, аспирантов, исследователей и всех, кто хочет больше узнать об углероде и включить углеродные материалы в новые приложения.»
Бюллетень MRS
Элементарные углеродные материалы имеют множество форм, включая графит, углеродное волокно, углеродные нанотрубки, графен, углеродную сажу, активированный уголь, фуллерен и алмаз. Эти формы сильно различаются по структуре, свойствам, способу изготовления и применению. Области применения этих форм углерода включают электронные, электромагнитные, электрохимические, экологические и биомедицинские приложения. Углеродные материалы являются предметом интенсивных исследований, имеющих большое значение как для науки, так и для технологий.
Эта книга представляет собой современный учебник по углеродным формам. Помимо вводной главы об углеродных материалах, книга включает главы о графите, графене, углеродной саже, активированном угле, углеродных волокнах и углеродных нановолокнах / нанотрубках. Например, глава о графите охватывает различные материалы из семейства графитов, включая поликристаллический графит, пиролитический графит, турбостратный углерод, интеркалированный графит, оксид графита, расслоенный графит и гибкий графит, в дополнение к их электронным и механическим свойствам.
Эта книга подходит для использования в качестве учебника для студентов и аспирантов в области естественных наук и инженерии, а также в качестве справочника для профессионалов. Он посвящен памяти руководителя докторской диссертации профессора М.С. Дрессельхауса (1930–2017) из Массачусетского технологического института.
Образец главы (ей)
Предисловие
Глава 1: Введение в углеродные материалы
Запросить копию для проверки
В комплекте:
- Введение в углеродные материалы
- Графит
- Графен
- Черный углерод
- Активированный уголь
- Углеродные волокна
- Углеродные нановолокна и нанотрубки
Аудитория: Студенты и аспиранты, а также специалисты, работающие с углеродными материалами.

«Множество иллюстраций делают эту книгу очень полезной для всех, кто пытается создать эти материалы. Общие практики, проиллюстрированные вместе с деталями и иллюстрациями оборудования, используемого для обработки материалов, делают эту книгу очень полезным справочником для работающих профессионалов, а также подходящий учебник для студентов и аспирантов материаловедения ».
IEEE Electrical Insulation Magazine
«Область углеродных материалов огромна и часто трудна для понимания, но эта книга легко читается и методично охватывает предмет, включая представление свойств материалов и данных о производительности с четкими иллюстрациями и графиками.Ссылки включают соответствующие старые и современные источники информации. Книга носит учебный характер и является отличным ресурсом для студентов старших курсов, аспирантов, исследователей и всех, кто хочет больше узнать об углероде и использовать углеродные материалы в новых приложениях ».
Бюллетень MRS
Окончательное руководство по проектированию и применению углеродного волокна
Почему следует использовать углеродное волокно вместо другого материала?Причина 1: Прочность
Основная причина, по которой можно было бы рассмотреть использование углеродного волокна, — это его высокое соотношение жесткости к весу. Углеродное волокно очень прочное, очень жесткое и относительно легкое.
Жесткость материала измеряется его модулем упругости . Модуль упругости углеродного волокна обычно составляет 34 MSI (234 ГПа). Предел прочности на разрыв углеродного волокна обычно составляет 600-700 KSI (4-4,8 ГПа). Сравните это с 2024-T3 Aluminium, который имеет модуль упругости всего 10 MSI и предел прочности на разрыв 65 KSI, или с 4130 Steel, у которого модуль упругости 30 MSI и предел прочности на растяжение 125 KSI.
Углеродное волокнос высоким и сверхвысоким модулем упругости или высокопрочное углеродное волокно также доступно благодаря улучшенным материалам и обработке углеродного волокна.
Деталь из композитного углеродного волокна представляет собой комбинацию углеродного волокна и смолы, которая обычно представляет собой эпоксидную смолу. Прочность и жесткость детали из углеродного волокна будут результатом совокупности прочности и жесткости как волокна, так и смолы. Величина и направление локальной прочности и жесткости композитной детали контролируются локальной плотностью и ориентацией волокон в ламинате.
В технике типично для количественной оценки преимущества конструкционного материала с точки зрения его отношения прочности к весу ( Удельная прочность ) и его отношения жесткости к массе (Удельная жесткость) , особенно если уменьшенный вес связан с улучшенными характеристиками или уменьшением Стоимость жизненного цикла.
Пластина из углеродного волокна, изготовленная из углеродного волокна полотняного переплетения со стандартным модулем упругости при сбалансированной и симметричной укладке 0/90, имеет модуль упругости при изгибе прибл.10 MSI. Его объемная плотность составляет около 0,050 фунта / дюйм3. Таким образом, отношение жесткости к весу или Удельная жесткость для этого материала составляет 200 MSI. Прочность этой пластины составляет прибл. 90 KSI, поэтому удельная прочность для этого материала составляет 1800 KSI
Для сравнения, модуль изгиба алюминия 6061 составляет 10 MSI, прочность — 35 KSI, а объемная плотность — 0,10 фунта. Это дает удельную жесткость , равную 100 MSI, и удельную прочность , равную 350 KSI.Сталь 4130 имеет жесткость 30 MSI, прочность 125 KSI и плотность 0,3 фунта / дюйм3. Это дает удельную жесткость , равную 100 MSI, и удельную прочность , равную 417 KSI.
Материал | Удельная жесткость | Удельная прочность |
Углеродное волокно | 200 МСИ | 1800 КСИ |
6061 Алюминий | 100 МСИ | 350 КСИ |
4130 Сталь | 100 МСИ | 417 КСИ |
Следовательно, даже основная панель из углеродного волокна с полотняным переплетением имеет удельную жесткость в 2 раза больше, чем алюминий или сталь.Он имеет удельную прочность в 5 раз больше, чем у алюминия, и в 4 раза больше, чем у стали.
Если рассматривать вариант индивидуальной настройки жесткости панели из углеродного волокна за счет стратегического размещения волокон и включать в себя значительное увеличение жесткости, которое возможно с сэндвич-структурами с использованием легких материалов сердцевины, становится ли очевидным преимущество, которое композиты из углеродного волокна могут создавать в самых разных областях применения. Конкретные цифры зависят от деталей конструкции и области применения.Например, сэндвич с пенопластом имеет чрезвычайно высокое отношение прочности к весу при изгибе, но не обязательно при сжатии или раздавливании. Кроме того, нагрузки и граничные условия для любых компонентов уникальны для конкретной конструкции. Таким образом, невозможно обеспечить толщину пластины из углеродного волокна, которая могла бы напрямую заменить стальную пластину в данном применении, без тщательного рассмотрения всех конструктивных факторов. Это достигается путем тщательного инженерного анализа и экспериментальной проверки.
Одним из примеров гибкости конструкции из углеродного волокна является индивидуальная конструкция балок с заданной жесткостью по определенным осям. Компания Element 6 Composites разработала запатентованные методы изготовления труб из углеродного волокна для обеспечения оптимальной жесткости по каждой оси изгиба. Такие трубы похожи на двутавровые балки по сопротивлению изгибу, но сохраняют высокую жесткость на кручение, присущую трубке.
Углерод / углеродные волокна и композитные материалы | Продукция
Это ссылки для перемещения по этой странице
Фильтр по приложениям
[Закрыть]
Mitsubishi ™ Coke — это сырье, используемое в доменных печах.Кокс получают путем смешивания многих видов угля и обугливания (коксования) при высокой температуре около 1200 ℃ в коксовой печи. Кокс является одним из основных сырьевых материалов для производства чугуна в доменных печах и поставляется на основные сталелитейные заводы Японии и других стран.
Игольчатый кокс используется в качестве основного материала для графитовых электродов в электропечи.Игольчатый кокс на угольной основе производится из каменноугольной смолы, которая образуется при производстве кокса.
По сравнению с игольчатым коксом на нефтяной основе игольчатый кокс на угольной основе обладает превосходными физическими свойствами, такими как низкий коэффициент теплового расширения и низкое электрическое сопротивление, а также меньшее растрескивание и меньшее разрушение. Номер CAS 94113-91-4
Пековый кокс производится из каменноугольной смолы, которая образуется при производстве кокса.
Пековый кокс является важным сырьем для строительного оборудования для производства полупроводников или панелей солнечных батарей.
Он также используется в качестве сырья для анода при выплавке алюминия.
CAS № 94113-91-4
DIAPOL ™ -WMB — это композитный материал (влажная маточная смесь), полученный путем кислотной коагуляции латекса SBR, углеродной сажи и водной суспензии в процессе ультрадисперсии.Широко применяется как сырье для промышленных товаров; гидрозатворы и прокладки; и шины и ремни.
DIABLACK ™ используется в качестве армирующего материала в широком диапазоне продуктов, таких как шины и резиновые изделия. Номер CAS 1333-86-4
MITSUBISHI ™ Проводящая сажа использовалась в качестве проводящего материала в широком диапазоне продуктов, таких как пленка, лотки для микросхем, нагревательный лист, магнитная лента и токопроводящая резина. Номер CAS 1333-86-4
MITSUBISHI ™ Carbon Black — это черный пигмент, который использовался в широком диапазоне областей, таких как газетная краска, печатная краска, цветная смола, краска, тонер, цветная бумага, индийские чернила и керамика.
Доступны различные марки технического углерода, от универсального до высококачественного. Кроме того, в нашу линейку продуктов входят промышленные и экологически чистые сажи.
- Номер CAS 1333-86-4
- Справочник ассоциации Carbon Black Association 3-е издание (Ref.1)
- Годовой отчет Ассоциации технического углерода № 61 (2011) (Ссылка 2)
Углеродное волокно — это высокопрочный материал с высоким модулем упругости, однако его удельный вес составляет всего одну четверть от веса железа. Таким образом, он обеспечивает высокую прочность, высокую жесткость и снижение веса в самых разных областях применения.
Жгут из углеродного волокна, состоящий из пучков нескрученных нитей, является основным материалом в нашей линейке продуктов из углеродного волокна.
Препрег из углеродного волокна — это промежуточный материал в виде листа углеродного волокна, пропитанного матричной смолой. Существуют различные типы препрегов, такие как препрег UD (однонаправленный препрег), в котором углерод волокна выровнены в одном направлении, и тканевый препрег, в котором углеродные волокна вплетены в ткань и пропитаны матричной смолой.
Углеродные ткани обладают отличными драпирующими свойствами, что делает их идеальными для создания трехмерных фигур. Благодаря своим выдающимся возможностям дизайна углеродные ткани также пользуются большим спросом в областях, требующих визуальной привлекательности. Углеродистые материалы не только обладают конструктивным потенциалом, но и обеспечивают превосходную эффективность укладки. Вы можете укладывать однослойный слой в двух направлениях.
Углеродное рубленое волокно — продукт, изготовленный путем измельчения жгута углеродного волокна.
Углеродное измельченное волокно — это продукт, получаемый путем измельчения измельченного волокна в порошкообразную (размолотую) форму.
Рубленое волокно обычно имеет длину от 3 до 6 мм, а измельченное волокно — менее 200 мкм. Оба эти материала используются для улучшения физических свойств термопластичных смол и каучуков, а также для увеличения электрической и теплопроводности.
По сравнению с обычными стальными пластинами или арматурой с бетонной оболочкой REPLARK упрощает строительство и сокращает сроки строительства, устраняя необходимость в тяжелой технике. Благодаря своей высокой прочности, легкости, долговечности и отличной обрабатываемости REPLARK заработал выдающуюся репутацию в области ремонта и усиления опор мостов, половиц, колонн, дымоходов и других конструкций.
e-Plate / Leadline: этот ремонтный и армирующий материал позволяет армировать, просто прикрепляя или заделывая сборные пластмассы, армированные углеродным волокном (CFRP), без необходимости пропитки смолой или наложения необходимого количества арматуры, как в случае ремонта и армирование листами из углеродного волокна, что сокращает время строительства и улучшает качество строительства.
Углеродное волокно FMC (CF-SMC) — это листовой промежуточный материал, изготовленный из обрезного высокопрочного углеродного волокна, пропитанного термореактивной смолой.Этот материал можно формовать под давлением, что значительно сокращает время формования по сравнению с обычным формованием в автоклаве или печи.
Кроме того, по сравнению с промежуточными углеродными волокнами из непрерывных волокон, случайное расположение коротких волокон обеспечивает текучесть и позволяет формовать детали сложной формы, например, с ребрами и выступами.
Гранулы из углеродного волокна — это термопластические формовочные материалы, созданные путем смешивания углеродного волокна с различными смолами для достижения характеристик, превосходящих обычные армированные смолы.Улучшенные физические свойства могут быть достигнуты путем комбинирования различных базовых смол и углеродных волокон в соответствии с конкретным применением.
GDL (Gas Diffusion Layer) — это основной материал газодиффузионного слоя для топливных элементов. Это продукт типа копировальной бумаги, разработанный на основе технологии углеродного волокна и композитных материалов.
Композитные материалы из углеродного волокна, также известные как пластмассы, армированные углеродным волокном (CFRP), представляют собой композитные материалы, изготовленные из углеродных волокон и смолы (в основном эпоксидной смолы).
Эти легкие, прочные и твердые материалы используются в широком диапазоне применений, таких как спортивные товары, промышленность, авиационные и автомобильные компоненты. Выбирая подходящую смолу, можно добавить такие характеристики, как термостойкость, ударопрочность и огнестойкость, и, таким образом, обеспечить превосходные характеристики, которых нет у обычных металлов и керамики, что позволяет снизить вес деталей и создать более свободную конструкцию.
Валы для гольфа — Углеродное волокно было разработано в качестве ведущего материала в области спортивного оборудования из-за его превосходной гибкости конструкции и превосходной термостойкости и ударопрочности. Доля валов CF на рынке валов для гольфа росла в течение многих лет, особенно благодаря высокому спросу на легковесы, и продолжает расти.
(валы CF производятся путем обертывания листов углеродного волокна, пропитанного эпоксидной смолой, известного как «препрег», вокруг металлического сердечника с последующим отверждением при высокой температуре.) Композиты
C / C (углерод, армированный углеродным волокном) изготовлены из углеродной матрицы, армированной углеродным волокном, и обладают высокой прочностью, высокой эластичностью, высокой вязкостью и сверхвысокой термостойкостью и могут использоваться при температурах выше 1000 ° C.
C / SiC, также известный как композит с керамической матрицей (CMC), представляет собой композитный материал с керамической матрицей, а наш CMC армирован углеродным волокном. Он имеет более высокую прочность и эластичность, чем композит C / C, и может использоваться в более широком спектре приложений.
CARBOLEADER® — угольный каток, который одновременно отличается малым весом, высокой жесткостью и большим критическим числом оборотов. Он используется для широкого спектра применений, включая сепараторы для аккумуляторных батарей, для оптики и для всех видов пленок, для печати и производства бумаги. Это может значительно повысить производительность и снизить затраты за счет улучшения качества и скорости производства, а также снижения количества брака.
Это конец страницы
Углеродное волокно: материал будущего?
Углеродное волокно — это длинная тонкая нить материала около 0.0002-0,0004 дюйма (0,005-0,010 мм) в диаметре и состоит в основном из атомов углерода. Атомы углерода связаны вместе в микроскопические кристаллы, которые более или менее выровнены параллельно длинной оси волокна. Выравнивание кристаллов делает волокно невероятно прочным для своего размера. Несколько тысяч углеродных волокон скручены вместе, образуя пряжу, которая может использоваться сама по себе или вплетаться в ткань. Пряжа или ткань комбинируют с эпоксидной смолой и наматывают или формуют в форму для образования различных композитных материалов.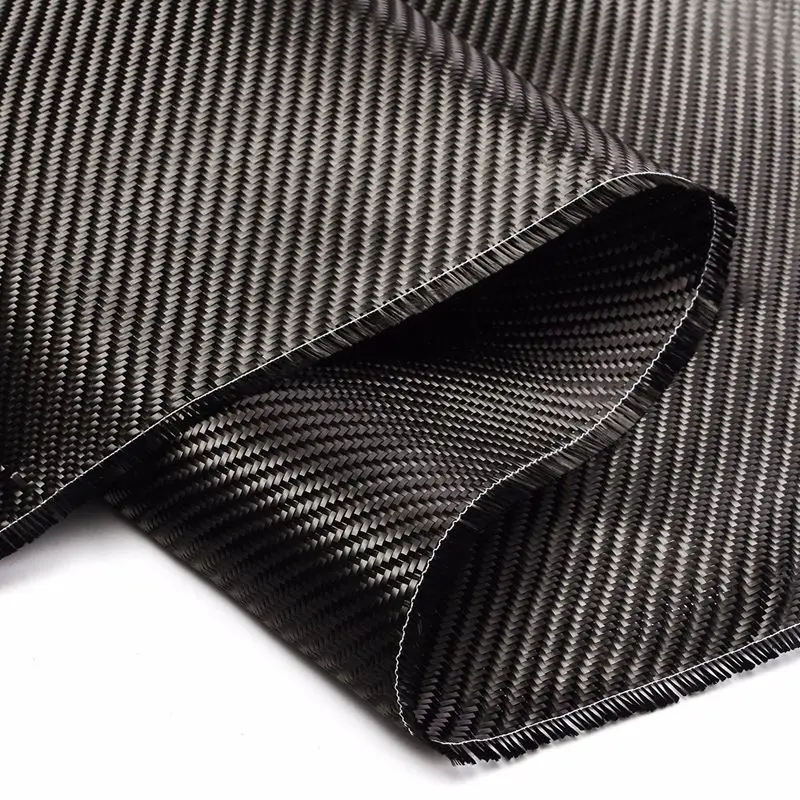
Углеродные волокна классифицируются по модулю упругости волокна. Английская единица измерения — фунты силы на квадратный дюйм площади поперечного сечения или фунты на квадратный дюйм. Углеродные волокна, классифицируемые как «низкомодульные», имеют модуль упругости ниже 34.8 миллионов фунтов на квадратный дюйм (240 миллионов кПа). Другие классификации в порядке возрастания модуля упругости при растяжении включают «стандартный модуль», «промежуточный модуль», «высокий модуль» и «сверхвысокий модуль». Углеродные волокна со сверхвысоким модулем имеют модуль упругости при растяжении 72,5–145,0 миллионов фунтов на квадратный дюйм (500–1,0 миллиарда кПа). Для сравнения, сталь имеет модуль упругости при растяжении около 29 миллионов фунтов на квадратный дюйм (200 миллионов кПа). Таким образом, самые прочные углеродные волокна в десять раз прочнее стали и в восемь раз больше алюминия, не говоря уже о том, что они намного легче обоих материалов, 5 и 1.5 раз соответственно. Кроме того, их усталостные свойства превосходят все известные металлические конструкции, и они являются одними из наиболее устойчивых к коррозии доступных материалов в сочетании с соответствующими смолами.
Тридцать лет назад углеродное волокно было материалом космической эры, слишком дорогим для использования в чем-либо, кроме аэрокосмической. Однако сегодня углеродное волокно используется в ветряных турбинах, автомобилях, спортивных товарах и во многих других областях. Благодаря производителям углеродного волокна, которые привержены концепции коммерциализации, заключающейся в расширении производственных мощностей, снижении затрат и расширении новых рынков, углеродное волокно стало жизнеспособным коммерческим продуктом.
Сырье, используемое для производства углеродного волокна, называется прекурсором. Около 90% производимых углеродных волокон производится из полиакрилонитрила (ПАН). Остальные 10% сделаны из искусственного шелка или нефтяного пека. Все эти материалы представляют собой органические полимеры, характеризующиеся длинными цепочками молекул, связанных вместе атомами углерода. Точный состав каждого прекурсора варьируется от одной компании к другой и обычно считается коммерческой тайной.
В процессе производства используются различные газы и жидкости.Некоторые из этих материалов предназначены для взаимодействия с волокном для достижения определенного эффекта. Другие материалы предназначены для того, чтобы не вступать в реакцию или предотвращать определенные реакции с волокном. Как и в случае с прекурсорами, точный состав многих из этих технологических материалов считается коммерческой тайной.
Процесс изготовления углеродных волокон частично химический, а частично механический. Прекурсор втягивается в длинные пряди или волокна, а затем нагревается до очень высокой температуры, не позволяя ему вступать в контакт с кислородом.Без кислорода волокно не может гореть. Вместо этого высокая температура заставляет атомы в волокне сильно вибрировать до тех пор, пока большинство неуглеродных атомов не будет вытеснено. Этот процесс называется карбонизацией, и в результате остается волокно, состоящее из длинных тесно связанных цепочек атомов углерода, и остается лишь несколько неуглеродных атомов.
История
Промышленность синтетического углерода официально началась в 1886 году с создания Национальной углеродной компании. Базирующаяся в Кливленде, штат Огайо, компания в конечном итоге слилась с Union Carbide в 1917 году и образовала Union Carbide & Carbon Corp., которая сменила название на Union Carbide Corp. в 1957 году. Подразделение углеродных продуктов Union Carbide Corp. стало независимой UCAR Carbon Company в 1995 году, а в 2002 году было переименовано в GrafTech International Holdings. конец 1800-х годов, когда угольные дуговые лампы начали освещать улицы крупных городов США. Лампы состояли из двух угольных стержней, подключенных к источнику тока и разделенных небольшим расстоянием. Пылающий горячий путь заряженных частиц — «дуга» — образовался между двумя стержнями, испуская интенсивный свет.Компания National Carbon начала свою деятельность с производства угольных электродов для уличных фонарей в центре Кливленда.
В 1879 году Томас Эдисон изобрел первую лампочку накаливания, в которой электричество нагревает тонкую полоску материала, называемую нитью накала, до тех пор, пока она не начнет светиться. Возможно, он также создал первое коммерческое углеродное волокно. Чтобы сделать свои первые волокна, Эдисон сформировал хлопковые нити или бамбуковые ленты нужного размера и формы, а затем запек их при высоких температурах. Хлопок и бамбук состоят в основном из целлюлозы, натурального линейного полимера, состоящего из повторяющихся звеньев глюкозы.При нагревании нить накаливания «карбонизировалась», становясь точной копией исходного материала — полностью углеродным волокном той же точной формы. Вольфрамовая проволока вскоре вытеснила эти углеродные нити, но они все еще использовались на кораблях ВМС США вплоть до 1960 года, потому что они выдерживали вибрации корабля лучше, чем вольфрам.
Можно ли создавать волокна из других неметаллических элементов? Какие химические или физические характеристики необходимы?
Чем этот материал лучше других синтетических волокон, известных своей прочностью, таких как вискоза, кевлар или стекловолокно? В каком приложении каждый из них преуспел? Какие соображения в этом приложении нам следует учитывать? И что заставит их не использовать их?
Обнаружен новый тип атомно-тонкого углеродного материала
Структура новой углеродной сети.В верхней части схематично показано соединение атомов углерода, образующих квадраты, шестиугольники и восьмиугольники. Нижняя часть — изображение сети, полученное с помощью микроскопии высокого разрешения. Предоставлено: Марбургский университет, Университет Аалто
.
Углерод существует в различных формах. Помимо алмаза и графита, недавно были обнаружены формы с удивительными свойствами. Например, графен толщиной всего в один атомный слой является самым тонким из известных материалов, а его необычные свойства делают его чрезвычайно привлекательным кандидатом для таких приложений, как электроника будущего и высокотехнологичная инженерия.В графене каждый атом углерода связан с тремя соседями, образуя шестиугольники, образующие сотовую сеть. Теоретические исследования показали, что атомы углерода могут также располагаться в других плоских схемах сети, при этом все еще связываясь с тремя соседями, но ни одна из этих предсказанных сетей не была реализована до сих пор.
Исследователи из Марбургского университета в Германии и Университета Аалто в Финляндии открыли новую углеродную сеть, которая атомарно тонка, как графен, но состоит из квадратов, шестиугольников и восьмиугольников, образующих упорядоченную решетку.Они подтвердили уникальную структуру сети с помощью сканирующей зондовой микроскопии и обнаружили, что ее электронные свойства сильно отличаются от свойств графена.
В отличие от графена и других форм углерода, новая бифениленовая сетка — как называется новый материал — обладает металлическими свойствами. Узкие полоски сетки, шириной всего 21 атом, уже ведут себя как металл, в то время как графен такого размера является полупроводником. «Эти полосы можно использовать в качестве проводников в будущих электронных устройствах на основе углерода.- сказал профессор Майкл Готфрид из Марбургского университета, возглавляющий группу разработчиков этой идеи. Ведущий автор исследования Цитанг Фан из Марбурга продолжает: «Эта новая углеродная сеть может также служить в качестве превосходного анодного материала в литий-ионных батареях с большей емкостью лития по сравнению с нынешними материалами на основе графена».
Команда из Университета Аалто помогла создать изображение материала и расшифровать его свойства. Группа профессора Питера Лилджерота провела микроскопию с высоким разрешением, которая показала структуру материала, в то время как исследователи под руководством профессора Адама Фостера использовали компьютерное моделирование и анализ, чтобы понять захватывающие электрические свойства материала.
Новый материал изготавливается путем сборки углеродсодержащих молекул на чрезвычайно гладкой золотой поверхности. Эти молекулы сначала образуют цепи, которые состоят из связанных шестиугольников, а последующая реакция соединяет эти цепи вместе, образуя квадраты и восьмиугольники. Важной особенностью цепочек является то, что они хиральные, что означает, что они существуют в двух типах зеркального отражения, таких как левая и правая рука. Только цепи одного типа собираются на поверхности золота, образуя упорядоченные сборки, прежде чем они соединятся.Это критически важно для образования нового углеродного материала, потому что реакция между двумя разными типами цепочек приводит только к графену. «Новая идея состоит в том, чтобы использовать молекулярные предшественники, которые настроены для получения бифенилена вместо графена», — объясняет Линхао Ян, который проводил эксперименты по микроскопии с высоким разрешением в Университете Аалто.
На данный момент команды работают над производством листов материала большего размера, чтобы можно было дополнительно изучить возможности его применения. Однако «Мы уверены, что этот новый метод синтеза приведет к открытию других новых углеродных сетей.- сказал профессор Лилиерот.
Ссылка: «Бифениленовая сеть: небензоидный углеродный аллотроп» Цитанг Фан, Линхао Ян, Маттиас В. Трипп, Ондрей Крейси, Ставрина Димостенус, Стефан Р. Качель, Менги Чен, Адам С. Фостер, Ульрих Кёрт, Питер Лильерот и Дж. Майкл Готфрид, 21 мая 2021 г., Science .
DOI: 10.1126 / science.abg4509
Углеродное волокно, армированное графеном, на 225% прочнее и на 184% жестче
Углеродное волокно — сверхпрочный, но легкий материал.Он в пять раз прочнее стали, в два раза жестче и примерно в 1,5 раза легче. Это идеальный материал для изготовления вещей, которые должны быть легче, но при этом должны быть прочными, например автомобилей, самолетов и спортивного инвентаря. Его тоже использовали бы намного больше, если бы его производство не было таким дорогим.
Теперь группа ученых из Университета штата Пенсильвания (в сотрудничестве с Университетом Вирджинии, Окриджской национальной лабораторией и отраслевыми партнерами Солвей и Ошкош) предложила новый способ создания материала, который не только удешевляет процесс, но и также укрепляет волокна. А волшебный ингредиент — излюбленный двумерный лист атомов углерода — графен. Команда надеется, что их открытие может привести к более широкому использованию углеродного волокна в производстве автомобилей, повышению их безопасности и снижению их стоимости.
Адри ван Дуин, профессор механической и химической инженерии в Пенсильвании и директор Центра вычисления материалов MRI, сказал:
Предоставлено: Маргарет Ковалик и Адри Ван Дуин / Penn StateНесмотря на то, что углеродные волокна обладают действительно хорошими характеристиками, они сделали бы автомобиль намного дороже, если бы углеродные волокна производились сейчас.Если вы сможете упростить производство этих свойств, вы сможете значительно облегчить автомобили, снизить их стоимость и сделать их более безопасными.
Углеродные волокна были основой производства самолетов на протяжении десятилетий. Но когда они переходят к другим приложениям, таким как велосипеды и автомобили, они производят только топовые продукты, слишком дорогие для большинства из них. Текущая рыночная цена на углеродное волокно составляет около 15 долларов США за фунт (0.45 кг). Прорыв команды может однажды снизить эту цифру до 5 долларов США.
Малгожата Ковалик, исследователь из Департамента машиностроения штата Пенсильвания, сказала:
В настоящее время большинство углеродных волокон производится из полимера, известного как полиакрилонитрил, или PAN, и это довольно дорого. Стоимость ПАН составляет около 50% от стоимости производства углеродных волокон.
Изготовление PAN требует огромного количества энергии из-за экстремальных температур, необходимых для превращения полимера в длинные прочные цепочки атомов углерода.Трехэтапный процесс включает нагревание волокон PAN при повышении температуры от 200-300 градусов Цельсия на первом этапе до 2100 градусов Цельсия на третьем. Первый этап окисляет нити, второй этап превращает атомы в углерод, а третий этап выравнивает молекулы должным образом. 90% доступных углеродных волокон производятся с использованием PAN.
Используя сочетание лабораторных экспериментов и компьютерного моделирования, исследователи добавили графен в углеродное волокно и проанализировали его свойства. Команда хотела выяснить, можно ли изменить процесс, чтобы меньше полагаться на PAN.Итак, они проверили, что произойдет, если они заменит его графеном. Они обнаружили, что добавление следовых количеств материала (концентрация всего 0,075% по весу) на первой стадии процесса значительно улучшило качество конечного продукта. Их углеродное волокно, пропитанное графеном, имело на 225% большую прочность и на 184% большую жесткость, чем углеродные волокна, изготовленные традиционным способом на основе PAN.
Их анализ показал, что это произошло потому, что плоская структура графена помогает последовательно выстраивать молекулы PAN по всем нитям.Кроме того, когда графен подвергается воздействию высоких температур, его края приобретают естественные каталитические свойства, вызывая конденсацию PAN вокруг этих краев.
Van Duin сказал:
Мы соединили эксперименты разных масштабов, чтобы не только показать, что этот процесс работает, но и дать нам атомистическую причину того, почему эти типы добавок работают.
Эти знания позволяют нам дополнительно оптимизировать процесс.
Следующее видео представляет собой компьютерную симуляцию добавления графена в первую фазу процесса выращивания углеродных волокон:
Впечатляющий прирост производительности побудил исследователей продолжить изучение потенциала графена (наряду с более дешевыми прекурсорами) в производственном процессе, чтобы, надеюсь, полностью удалить некоторые этапы, тем самым еще больше снизив затраты.
Между тем, есть несколько других интересных способов использования графена, например, для создания более безопасных красок для волос, для покрытия лицевых масок и их защиты от вирусов, для очистки воздуха и для усиления переработанного резинового материала для изготовления прочных полов.
Композитный строительный материал прочнее стали
- Углеродное волокно — более легкая альтернатива стали, которая в пять раз прочнее и в два раза жестче.
- Методы изготовления позволяют продемонстрировать красоту и уникальные свойства углеродистой стали за счет необычной геометрии.
- Углеродное волокно идеально подходит для крупнопролетных конструкций, таких как крыши стадионов; перспективный метод изготовления — кабельные роботы.
В любой будний день деловой район Луп в центре Чикаго изобилует измученными людьми, переходящими улицу, словно стада диких антилоп, спасающихся от хищника. Большинство суетятся мимо Полевого здания, не задумываясь о его значении, или исторического здания, снесенного в 1931 году на том же месте: Дом страхования жилья.Построенное в 1884 году, это было первое высокое здание, возведенное на каркасе из конструкционной стали — легкого, доступного и прочного материала, позволяющего возводить конструкции выше, прочнее и быстрее, чем из дерева или камня.
Считающийся первым в мире небоскребом, Дом страхования жилья навсегда изменил ход архитектуры, инженерии и строительства, продемонстрировав, что сталь является жизнеспособным строительным материалом, а конструкция из стального каркаса — жизнеспособной техникой. Он был всего 10 этажей (138 футов) в высоту, но был предшественником всех высоких зданий, построенных с тех пор, включая самое высокое здание в мире: Бурдж-Халифа в Дубае, высотой 206 этажей и высотой более полумили.
Спустя более 130 лет сталь и стальной каркас остаются королем строительства небоскребов. Но инновации в композитных материалах из углеродного волокна и в технологиях производства роботов могут означать, что новый деспот скоро свергнет их. И если исследование, проводимое в Технологическом центре Autodesk в Бостоне, является каким-либо показателем, оно может иметь столь же преобразующий характер.
Члены проектной группы Ибаньеса Кима вручную ткут нити из углеродного волокна в Технологическом центре Autodesk в Бостоне.
Углеродное волокно — один из самых перспективных композитных строительных материалов будущего. Полимер, состоящий из длинных тонких нитей атомов углерода, связанных вместе в кристаллическое образование — каждая нить тоньше человеческого волоса — он легче стали, в пять раз прочнее и в два раза жестче. Таким образом, он особенно популярен среди производителей, которые скручивают его пряди вместе, как пряжу, из которой можно соткать ткань или придать ей постоянную форму.Этот процесс используется для всего: от рамы велосипедов, удочек и крыльев самолетов до кузовов гоночных автомобилей, валов гольф-клубов и мачт для парусных лодок.
«Углеродное волокно и другие композитные материалы обладают высокой производительностью, что означает, что они имеют очень малый вес, но могут выдерживать огромные нагрузки», — говорит архитектор и недавний резидент Autodesk Technology Center Саймон Ким, директор Ibañez Kim, архитектурной и дизайнерской фирмы в Кембридже. MA.
Поскольку углеродное волокно обладает такими уникальными свойствами, Ким и другие считают его идеальным строительным материалом.«Композитные материалы представляют собой очень интересную возможность для быстрого изготовления и настройки», — говорит Ким, добавляя, что создание корпуса для небольшого дома из углеродного волокна займет всего несколько недель, по сравнению с месяцами при использовании обычных материалов. «Композитные конструкции могут быть возведены довольно быстро и не требуют особых затрат труда и рабочих потоков — например, от генеральных подрядчиков и субподрядчиков до поставок материалов. Таким образом, мы можем работать быстрее, цепочка поставок короче, количество материалов сокращается и это дешевле.”
Благодаря своей гибкости и легкому весу углеродное волокно можно легко перемещать. «Модули можно подбирать, брать в другом месте и связывать вместе, чтобы при необходимости производить более крупные сборки», — говорит он. «Это делает композитные конструкции намного более гибкими, чем традиционные здания, в которых предполагается постоянство, что не всегда хорошо».
Производственная установка в Технологическом центре Autodesk в Бостоне. Предоставлено Штутгартским университетом.
Технологии строительства из углеродного волокна позволяют создавать будущееПоявление стали не привело к появлению небоскребов.Чтобы использовать преимущества стали, архитекторам также потребовалась новая строительная техника: конструкция из стального каркаса. То же самое и с инновационными материалами, такими как углеродное волокно: его потенциал зависит от разработки передовых методов производства, которые позволят преодолеть разрыв между лабораториями и рабочими площадками.
Во время своего недавнего пребывания в Технологическом центре Ким и другие жители Аюб Лхарчи и Йенченг Лу, аспиранты Штутгартского университета, протестировали и продемонстрировали методы строительства из углеродного волокна.Их работа предвещает будущее, в котором архитектурные аргументы в пользу композитов будут прочнее стали, а точнее сказать, прочнее.
Ким начал свою резиденцию в Бостоне в июне 2017 года. Его цель: продемонстрировать, что конструкция из углеродного волокна может обеспечивать не только превосходную функциональность, но и превосходную форму. Его эксперименты — например, оценка прочностных свойств различных смол для создания композитов из полимеров, армированных углеродным волокном (CFRP) — используются в его установках в реальном мире.
«Мы используем временную конструкцию, чтобы не только продемонстрировать функциональные возможности углеродного волокна, но и показать, что оно культурно красиво», — говорит Ким. Он подчеркнул визуальные и тактильные качества конструкций из углепластика в «Лесу звука», проекте, финансируемом Pew, который он завершил вместе с оперным композитором Лембитом Бичером для его мировой премьеры оперы Sophia’s Forest . Представленная в сентябре 2017 года в Филадельфии опера представляет собой девять «звуковых скульптур», созданных Кимом и его командой Технологического центра. Каждый размером с человека-исполнителя, состоит из раны из углеродного волокна, в которой находится механизированный инструмент, создающий окружающие звуки во время выступления.
01/03
В Бостоне архитектор Саймон Ким и аспиранты Штутгартского университета Аюб Ларчи и Йенченг Лу протестировали методы производства углеродного волокна. Предоставлено Штутгартским университетом.
01/03
В основе процесса производства углеродного волокна лежал робот для плетения волокна. Предоставлено Штутгартским университетом.
01/03
Деталь робота, используемого в процессе изготовления. Предоставлено Штутгартским университетом.
По словам Кима, портативные скульптуры, хотя и построены в небольших масштабах, напоминающие паутину или коконы, намекают на архитектурный потенциал углеродного волокна. Он предвидит будущее, в котором существующие конструкции, такие как склады с контролируемым климатом, будут перепрофилированы путем добавления капсул или капсул из углеродного волокна. По сути, внешний вид здания останется стабильным, но интерьер можно будет настроить с помощью модульных офисов или жилых домов, изготовленных с использованием тех же процессов и принципов, что и звуковые скульптуры Кима.
«Мы можем строить новые объекты, но мы также должны осознавать тот факт, что у нас есть сотни лет существующего строительства, которое никуда не денется», — говорит Ким. «Сносить эти здания из бетона, кирпича и каменных панелей и восстанавливать их сложно с точки зрения компенсации энергопотребления и воздействия на окружающую среду. Почему бы не изменить их назначение и не модернизировать их функции с помощью «вставок», которые очень хорошо продуманы, легки и доступны по цене? »
Формируя будущее производства из углеродного волокна Мир природы полон интересной геометрии, от спиралей и сфер до кривых и конусов.И все же построенный мир слишком часто состоит из треугольников, кругов и квадратов. Стремясь открыть более широкий каталог возможных форм для построенных объектов, Ларчи и Лу потратили свою резиденцию в Бостоне, исследуя геометрический потенциал армированных волокном композитов (FRC).
По словам Лхарчи, для создания новой геометрии с использованием FRC, включая углеродные, стеклянные и арамидные волокна, требуется эффективный метод изготовления.«Лучше всего волокно использовать для крупнопролетных конструкций — например, когда вы хотите покрыть крышу стадиона и не хотите, чтобы колонны блокировали пространство внизу», — говорит он. «Если вы хотите построить что-то подобное в настоящее время, вы можете использовать либо большую машину, подобную тем, которые они используют для создания 3D-печатных домов, что я с трудом могу представить на месте, либо промышленный робот-манипулятор, где вы ограничены. насколько далеко может дотянуться рука. Что мы пытаемся сделать, так это найти метод изготовления, который будет практичным для построения одной непрерывной крупномасштабной структуры [FRC].”
Один из многообещающих методов производства углеродного волокна использует кабельных роботов, говорит Ларчи. Его команда продемонстрировала перспективы кабельных роботов в Технологическом центре, где он использовал веревку, чтобы имитировать поведенческие свойства углеродного волокна.
«Если вы когда-нибудь видели скайкамер на стадионе, то это, по сути, кабельный робот с камерой на нем», — говорит Ларчи, который разработал систему из двух кабельных роботов, работающих параллельно, один над другим. По мере того, как они пересекают кабель, роботы обмениваются волокном взад и вперед, переплетая его таким образом, чтобы обеспечить уникальную геометрию, такую как синтаксис намотки.«В любое время, когда вам нужно создать большую и легкую структуру, волокно — хороший выбор», — говорит он. «Я надеюсь, что, исследуя дешевые и доступные методы изготовления, мы сможем сделать производство волокна на месте основным направлением».
Эта статья была обновлена. Первоначально он был опубликован в декабре 2017 года.
Мэтт Олдертон — писатель-фрилансер из Чикаго, специализирующийся на бизнесе, дизайне, еде, путешествиях и технологиях.